Aft Structure - Thrust Manifold

At Boston University, I joined BURPG, a college rocket team with the goal of sending a custom-built rocket to space. Our rocket, dubbed Starscraper, is a 30 foot long, liquid propelled, thrust vector controlled beast which is aiming to hit 400,000 feet by summer 2017. It’s powered by two liquid fuel based engines which provide a combined 3000 lbs of thrust.
In order for the rocket to maintain a stable heading, the thrust produced by its engines needs to be directed at an angle to the rocket’s axis in order to correct for any deviations from the rocket’s flight path. There are two methods by which this could happen, Liquid Injection Thrust Vector Control (LITVC) or Gimbaling. In LITVC, fuel is injected into the engine or combustion chamber at different angles to produce variations in the direction that the thrust leaves the engine. In a gimbaled approach, the entire engine is rotated about the rocket’s axis in any direction to change the direction of the thrust. We chose the gimbaling method to solve this problem. One of the drawbacks of gimbaling is that the plumbing or the tubing system that delivers the fuel and the oxidizer to the engine becomes very intricate. To simplify and better integrate this plumbing, I designed a custom made thrust manifold that combined several functions in the engine section into a single assembly simplifying the plumbing significantly.The Thrust Manifold internally split a single oxidizer (OX) feed line into two separate channels that delivered OX flow to each engine.
Design Requirements
- Flow
- Minimal interruption to flow of OX from MOX feed to OX dome
- OX channel should maintain ¾” diameter
- Dimensions
- Should match engine profile
- Thickness of overall manifold <= 1.5”
- Mounting
- Should be able to mount ring joint yokes as well as attach to ox-dome
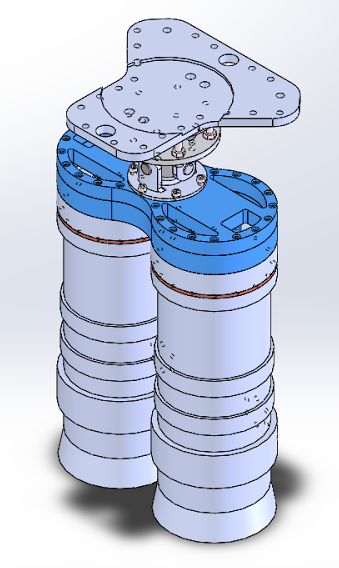
Flow Analysis

- Resolved flow separation issues by arcing channel from center plane to outlet
- Analysis indicates limited flow separation around outlet
- Input pressure: 900 PSI, Output Pressure: 400 PSI
Stress Analysis
- 6061 Aluminum: 35,000 PSI yield strength
- hand calc stress across base: 500 PSI
- Max von mises stress: 741 PSI
- Factor of safety based on hand calc: 70
- Factor of safety based on solidworks: 47
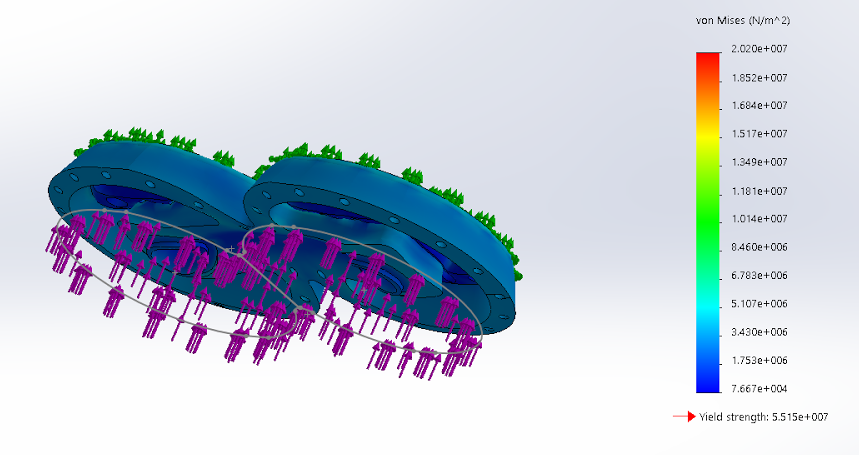
Sealing
- Face seal between two sections can use standard o-ring according to parker representative.
- AS568B-206 o-ring for static industrial phase seal against ox-dome
- Sealing and connection to MOX feed TBD based on bellows